Integrated Robotics, Welding and Vision System
Liburdi's years of experience and practical expertise in the repair of turbine components provide the unique insight required for the successful design and integration of the tooling, the axis, the vision, the power supply and the controller. 'Turn-Key' systems include the development of the weld process, NDT examination, metallurgical certification, training and start-up. |
Features
Proven track record of welding critical turbine components - HPT blades, shrouded LPM™ blades, compressor blades and seals. Systems in service at major airlines, component repair facilities, and military overhaul facilities since 1990. Systems and processes developed for all high strength alloys, equiaxed, directional and single crystal castings.
Liburdi Vision System™ (LVS)
Proven 3-dimensional imaging and processing to derive torch path and weld parameters in less than 1 second. Vision is fully integrated with PC based Liburdi Robotic Controller™ (LRC). Real time monitoring during welding is available with video playback.
Liburdi Robotic Controller™(LRC)
Powerful PC based controller for high reliability and ease of maintenance. Incorporates graphic display features for critical weld parameters and easy to use English language programming. Custom hand held pendant designed specifically for welding.
Liburdi Pulsweld® Welding Power Source
Available with integral 50, 100 or 200 Amp precision power source configured for GTAW, PAW or Variable Polarity pulse welding with assured repeatability and accuracy for critical welding applications.
Automation Support
Liburdi Automation provides single source design and support responsibility for all robotic motion systems, vision systems, welding power supplies and advanced controllers. Complete engineering support is also available to develop weld parameters, inspect the welds and perform the required metallurgical tests to qualify the weld process.
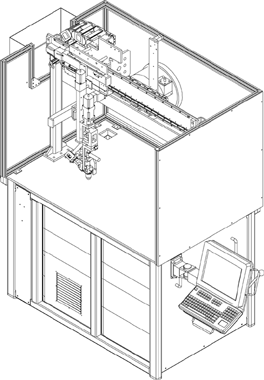
|
System Specifications
Physical Characteristics
Configuration: Overhead Gantry Architecture
Height: 79" (200 cm); 98" (250 cm) including wire bundle
Length: 63" (160 cm); 91" (231 cm) including keyboard
Width: 38" (97 cm)
Weight: 1500 lbs (1815 kg)
Number of Axes: 4 Standard Stepper Axis (X,Y,Z,W)for overhead torch motion. Additional rotary and tilt axis available on table as an option
Servo Axis Specifications
Axis |
Travel |
Velocity |
Repeatability |
X |
9.8" (25cm) |
40 IPM (17 mm/sec) |
± .001" (± .025 mm) |
Y |
9.8" (25cm) |
40 IPM (17 mm/sec) |
± .001" (± .025 mm) |
Z |
8.8" (22cm) |
40 IPM (17 mm/sec) |
± .001" (± .025 mm) |
W |
170° |
1000 DPM |
0.1° |
X (Manual) |
36" (91cm) |
Manual |
2" increments |
 |
|
Utilities |
Primary Voltage: 230 VAC - Three Phase
Current: 50/60 Hz @ 30 amp
Argon: 30 psi (regulated) (200 kPa)
Air: 80 psi (for optional tooling) (550 kPa) |
|
|
Welding Power Supply Specifications
Standard: Liburdi Pulsweld® P200 GTAW Power Source
Current: 0.1 - 200 Amps - 0.5% peak-to-peak ripple
Accuracy: 1% of full scale
Power: 2 kW average
Duty Cycle: Continuous 100%
Pulsation: Up to 20 KHz
Optional: 200 Amp GTAW/PAW current sources in Straight and Variable Polarity and LASER |
|
|
Standard Features
WinLAWS™ software
Liburdi DSP I/O with up to 20 KHz pulsing
Coordinated Motion
Three solenoid controlled gas lines with flow sensors
LCD touch screen and standard keyboard interface
Hand Held Operator Pendant
Closed circuit water cooler for torch |
|
|
Optional Accessories
Plasma or GTAW welding power supply
Variable polarity power supply
Real time weld monitoring and video playback
Laser Seam Tracker
Mass flow controllers for Plasma gas systems
Off-line computer programming
Tooling design and weld development
Service Plus; Bronze, Silver, Gold |
|